Understanding Injection Moldable Plastics: Revolutionizing the Future of Manufacturing
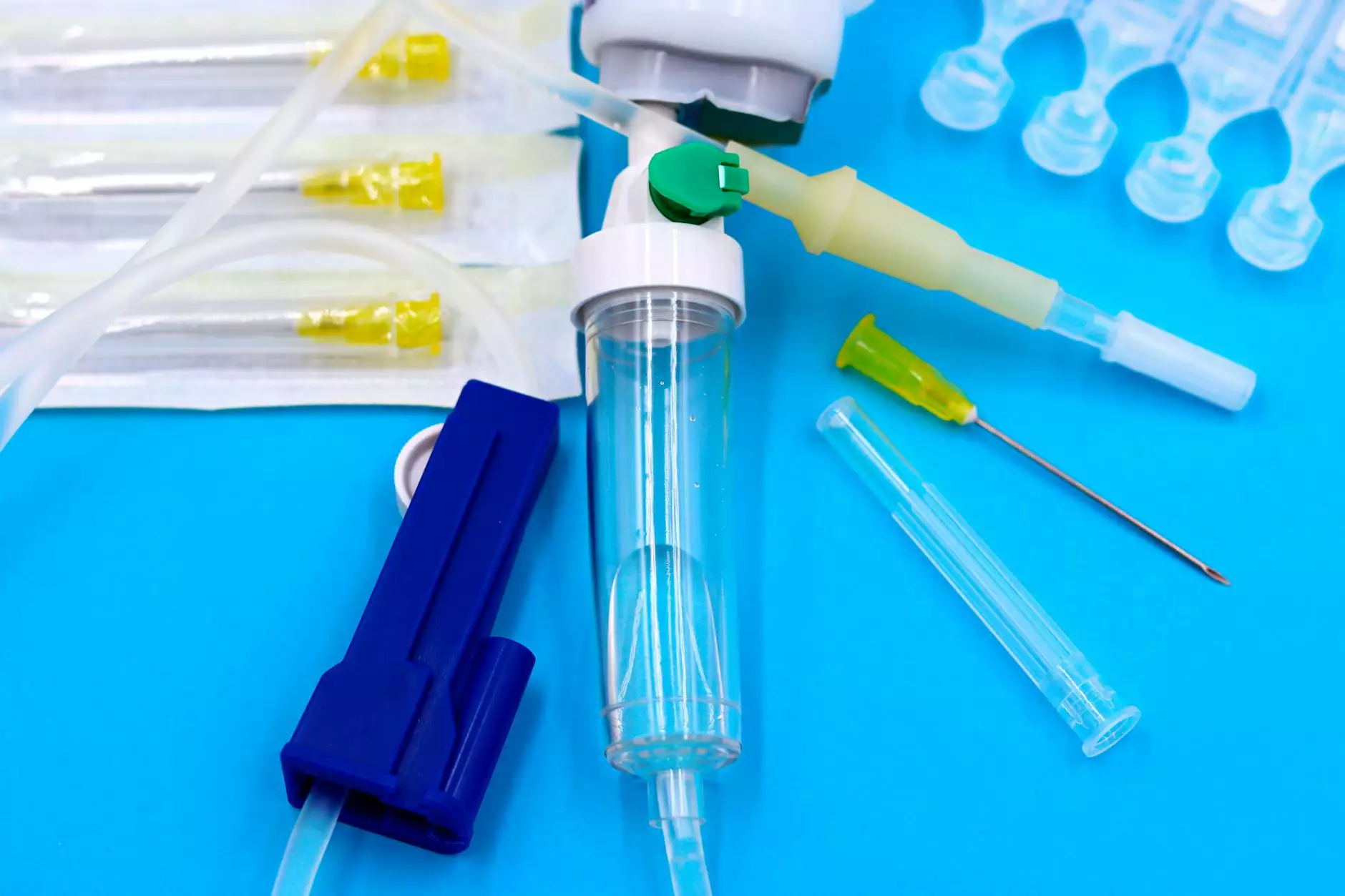
Injection moldable plastics have become a cornerstone in the manufacturing sector, revolutionizing how various industries approach production and design. Their versatility, coupled with advancements in technology, has led to an explosion of capabilities, making them an essential material for countless products. In this article, we will dive deeply into the world of injection moldable plastics, exploring their benefits, applications, and the future trends shaping this dynamic field.
What are Injection Moldable Plastics?
Injection moldable plastics refer to a category of thermoplastic materials that are utilized in the injection molding process. This method involves melting plastic pellets and injecting the molten material into a pre-designed mold where it solidifies. The result is a precise and often intricate part that is ready for various applications.
The Composition of Injection Moldable Plastics
These plastics are typically composed of the following elements:
- Base polymer: The primary component, often polycarbonate, polypropylene, or nylon.
- Additives: Substances such as colorants, stabilizers, and fillers enhance the properties of the plastic.
- Reinforcements: Materials like glass fibers or carbon fibers can be added to improve strength and rigidity.
The Advantages of Injection Moldable Plastics
The popularity of injection moldable plastics can be attributed to a range of significant advantages:
1. Cost-Effectiveness
Once the initial mold is created, injection molding allows for the mass production of parts at a low cost per unit. This is particularly advantageous for high-volume production runs.
2. Versatility in Design
Injection moldable plastics can be tailored to meet specific requirements, due to their ability to be molded into virtually any shape or size. This versatility allows designers to create complex geometries and features.
3. Superior Surface Finish
This process produces a high-quality surface finish, which reduces the need for additional processing steps like sanding or polishing.
4. Consistency and Reproducibility
Injection molding ensures that each part manufactured is uniform, providing reliability and consistency across production batches.
5. Wide Range of Material Options
There is a vast selection of injection moldable plastics available, each with unique properties suitable for different applications, such as:
- Polyethylene: Known for its flexibility and toughness.
- ABS: Offers excellent impact resistance and good dimensional stability.
- Polypropylene: Features robustness and chemical resistance.
Applications of Injection Moldable Plastics
Injection moldable plastics are used in various industries, each benefiting from their unique properties. Here are some key sectors:
1. Automotive Industry
In the automotive sector, lightweight and durable parts made from injection moldable plastics contribute to improved fuel efficiency and overall vehicle performance. Components such as dashboards, panels, and even engine parts encapsulate the advantages of these materials.
2. Consumer Products
From household goods to electronics, injection molding enables the mass production of high-quality consumer products. Baby toys, kitchen utensils, and mobile phone cases are prime examples of how these plastics are employed to enhance everyday life.
3. Medical Devices
Injection moldable plastics play a critical role in the medical field. They are used for creating durable and sterile components in devices like syringes, surgical instruments, and protective coverings, ensuring safety and reliability in healthcare applications.
4. Industrial Applications
In industrial settings, injection molded parts are often used for assembly line components and machinery housing, offering non-corrosive and durable solutions that withstand tough environments.
The Future of Injection Moldable Plastics
As technology advances, the future of injection moldable plastics continues to evolve. Here are some emerging trends to watch for:
1. Sustainable Materials
With the increasing emphasis on sustainability, the industry is focusing on developing biodegradable and recyclable injection moldable plastics. This shift will not only help reduce environmental impact but also meet consumer demand for eco-friendly products.
2. Smart Plastics
The integration of electronics into plastic components is on the rise. Smart plastics can change properties based on environmental stimuli, providing functionalities previously unattainable.
3. Advanced Manufacturing Techniques
Innovations in injection molding, such as 3D printing and AI-driven mold design processes, will lead to greater customization and efficiency in production.
Challenges in Injection Molding
While the benefits of injection moldable plastics are clear, the process is not without its challenges:
1. Initial Setup Costs
Creating high-quality molds can be expensive and time-consuming, which may deter some businesses from opting for injection molding, especially if they require low production runs.
2. Design Limitations
Although highly versatile, some complex designs may not be feasible using traditional injection molding methods, requiring innovative workaround solutions.
3. Material Constraints
Not all plastics are suitable for injection molding, and choosing the correct material for specific applications is crucial for ensuring that the desired characteristics of the final product are achieved.
Conclusion
In conclusion, the realm of injection moldable plastics is a vibrant and continually advancing domain within the manufacturing landscape. With their array of benefits, broad applications, and growing innovations, they present numerous opportunities for businesses seeking efficient and effective manufacturing solutions. Companies like Sumiparts are at the forefront of this industry, providing essential services in machining, laser cutting, welding, and plastic injection, thus ensuring that businesses can achieve their manufacturing goals while utilizing these remarkable materials. The future looks bright for injection moldable plastics, and as we continue to explore their potential, one thing becomes clear: they are here to stay, shaping the future of manufacturing for years to come.